Growing craft breweries need to straddle a line between their local heritage and a modern, scalable, nationwide operation. Each batch requires care and a hands-on approach for even the largest craft brewer. Maintaining that ethos while also producing and moving enough brew to enter five states, and then 10 states, and then 25 states and so on is a delicate equation. Successful craft brewers know that the best way to achieve this is by identifying areas of the process that can be streamlined or automated — without detracting from taste, experience or concept.
One of those areas is at the end of the line. Packaging is an important part of the overall operation, but its best handled by an automated solution when your production volumes and future outlook justify the initial equipment investment. As an example how to move to an automated packaging solution, let’s look at the story of Boulevard Brewing, which replaced its manual palletizing operations with a conventional automated palletizing system.
Boulevard Brewing case study
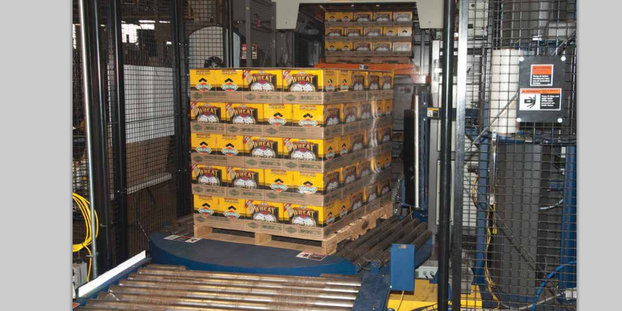
Sure, Boulevard is a larger brewery these days, recently purchased by Duvel, but it started in a 5-gallon kettle in a converted railroad building by John McDonald. Soon, McDonald’s homebrewing operation grew into a more serious business, and over 20 years, Boulevard Brewing Co. expanded its distribution from across town to across the country. And along that journey, they outgrew their equipment and needed to expand. McDonald had to make decisions to facilitate the next stage of company growth.
Boulevard eventually built a new three-story building adjacent to the original building that would include a 150-barrel brewhouse and a state-of-the-art $6 million bottling line. The project’s budget was calculated based on payback for the increased efficiency and throughput rate of the new line.
But all of these steps forward just lead to more questions and required more decisions. The most pressing at that point was the end of the line. Boulevard’s manual palletizing created a serious bottleneck for production, what you might call the classic I Love Lucy chocolate factory dilemma (or the lesser Saved By The Bell spaghetti sauce dilemma). With 11 workers on the floor, the facility produced about 300 bottles per minute. Three workers alternated the manual end-of-line palletizing, stacking cases weighing up to 30 pounds each at a rate of 12 cases per minute. After other efficiencies were gained throughout the line, it was clear the end of the line was not going to keep up.
The line is capable of brewery growth, with the capacity to quadruple the current operational capacity. It can also provide Boulevard with the ability to add second or third shifts if needed, or new patterns for future products.The brewery also needed a solution that had gentle handling and a compact footprint. The most prominent concern when palletizing cases of glass bottles is the machine’s ability to move and configure cases without shattering the product. Compounding this issue is the trend of bottle thinning, where glass thickness is decreased for both cost and environmental issues. With no corrugated partitions and progressively weaker glass, Boulevard knew that gentle manipulation of product would be a top priority.
And as for the space constraints, the facility was located in an urban, completely developed area just south of downtown that gave it a limited footprint to build on. Every piece of equipment needed to be compact, functional and efficient in both its use of space and process.
Boulevard turned to Intelligrated to help solve these issues, and Intelligrated recommended the Alvey 780 conventional palletizer for maximizing space efficiency and for gentle product handling. Particularly suited for single-line applications in the beverage industry and capable of rates of 50 cases per minute, the Alvey 780 provided the mid-speed rates that Boulevard needed. Additionally, with a 90-degree angle of the infeed conveyor, the Alvey 780 ensured the most compact footprint for the tight configuration of the facility.
The palletizing cell of the system was also designed to take advantage of dual-purpose functionality, where only one operator manages all functions of both the palletizing and depalletizing process.
Cases containing glass bottles in 6-pack, 12-pack and 20-pack configurations, as well as a 24-pack case of aluminum bottles, are conveyed to the high-level infeed of the Alvey 780 palletizer. After each layer of cases is placed on the pallet, the pallet lowers one layer. When the pallet is filled, it discharges from the machine at floor level via a full pallet conveyor provided by Intelligrated. Full pallets are conveyed along Intelligrated chain-driven live roller full pallet conveyor to a Lantech Q-series semi-automatic turntable and stretchwrapper, also provided by Intelligrated.
Since that implementation, the entire operation has moved from 11 workers running a maximum of 300 bottles per minute to five workers bottling 500 bottles per minute. A total of 25 to 30 cases are palletized by the Alvey 780 per minute, a 100 percent increase over Boulevard’s previous manual palletizing methods. The line is capable of brewery growth, with the capacity to quadruple the current operational capacity. It can also provide Boulevard with the ability to add second or third shifts if needed, or new patterns for future products.

More on Intelligrated Automation
At this year’s Craft Brewers Conference and BrewExpo America, we stopped by the Intelligrated booth to chat with Craig Merton, senior sales engineer, and Steve Cohron, sales account manager, about automation. Intelligrated offers tons of conventional and robotic automated solutions for a dozen industries that increase productivity and efficiency in their manufacturing, warehousing and distribution processes.
For breweries looking to step up their line efficiency, Intelligrated recommends:
-
Automating conveyor lines
-
Implementing conventional or robotic automated depalletizing solutions for incoming raw materials or empty containers. (Sometimes vision systems are also needed for this application.)
-
Robotic case unpacking of empty containers pre-filling line
-
Robotic singulation of empty containers pre-filling line
-
Robotic case re-packing of empty containers post-filling line
-
Automated sortation
-
Automated palletizers and depalletizers, robotic palletizing and depalletizing solutions, as well as hybrid palletizers that integrate one or more robotic arms with a conventional automated palletizer for improved product handling flexibility.
Intelligrated’s robotic solutions feature arms from multiple manufacturers, as well as standard and custom end-of-arm tooling designed and built in-house. The robotic systems are designed for gentle handling, whether it’s to gently unload product in preparation for fill lines or to reload product into cases before end-of-line palletizing. These robotic case packing and unpacking solutions can offer reduced breakage compared to manual drop packing and also save those precious man hours for areas of the brewery that could use them much more.
Alvey robotics solutions can operate on industry-standard PLC-based controls, enabling seamless integration with other line equipment and allowing facility personnel to support robotic applications from a familiar control platform and reducing total cost of ownership. For lower throughput operations, a single robot can execute both packing and unpacking, while high-throughput configurations assign dedicated robots to each task. Scalable solutions maximize efficiency and cost savings through increased uptime, reliability and efficiency for single-facility operations to multi-site enterprises.
Intelligrated also integrates visions systems with some applications, primarily for robotic depalletizing applications and for track and trace purposes and/or inventory management. Think supplementation to Alvey robotic keg handling (palletizing/depalletizing) solutions with the addition of tracking full ones that go out the door as well as returning empties.
For more information on these solutions, specifically on the distinction between conventional, robotic and hybrid palletizers, check out this white paper from Intelligrated.
More on conveying/palletizing from the Craft Brewing Business archives…
Packaging Equipment Reviewed: Conveying systems and accumulation tables
Getting beer to bottle is not as easy as it seems. Automated packaging requires transit — conveying, merging, diverting, picking, placing, transferring, orienting, stacking and every other gerund in between… Read More
Cablevey to exhibit kinetic display moving barley in real time: CBC Preview
Cablevey Conveyors will exhibit its kinetic display, which will move barley in real time during the Craft Brewers Conference and BrewExpo America. Cablevey Conveyors gently move products like grain, barley … Read More
Watch how Garvey Infinity Accumulation Tables work
For companies that spend a lot of time and money making a perfect brew, then spend just as much time designing the bottle labels and marketing the product, it is … Read More
RT @Intelligrated: From @CraftBrewingBiz: Automated craft beer packaging: http://t.co/xtelMAMdou A case study, tips from @Boulevard_Beer
RT @CraftBrewingBiz: Automated craft beer packaging http://t.co/tgdcV922sk A case study from @Boulevard_Beer, @Intelligrated #sundayreading
RT @CraftBrewingBiz: Automated craft beer packaging http://t.co/tgdcV922sk A case study from @Boulevard_Beer, @Intelligrated #sundayreading
RT @CraftBrewingBiz: Automated craft beer packaging http://t.co/tgdcV922sk A case study from @Boulevard_Beer, @Intelligrated #sundayreading
RT @Intelligrated: From @CraftBrewingBiz: Automated craft beer packaging: http://t.co/xtelMAMdou A case study, tips from @Boulevard_Beer
From @CraftBrewingBiz: Automated craft beer packaging: http://t.co/xtelMAMdou A case study, tips from @Boulevard_Beer
@CraftBrewingBiz Thanks for the mention! Great article!
RT @crsimp01: Automated craft beer packaging: Boulevard Brewing case study http://t.co/M2sHYlWej3
Automated craft beer packaging: Boulevard Brewing case study http://t.co/M2sHYlWej3
RT @CraftBrewingBiz: Automated craft beer packaging: http://t.co/tgdcV922sk A case study, tips from @Boulevard_Beer, @Intelligrated