
For almost three years now, a CO2 squeeze has limited supply and made usage more expensive depending on the season and the region. This has pushed many craft breweries to find alternatives to beverage-grade CO2, like employing nitrogen in some applications (it’s cheaper and easier to get, depending on your purity standards, and easier to create with a generator). But nitrogen is not a one-for-one swap for CO2.
“Nitrogen behaves very differently,” cautioned Chuck Skypeck, technical brewing projects director at the Brewers Association. Nitrogen is interesting, and we’ll discuss nitrogen alternatives in part 5 of this series.
But there is another option sitting right under a brewer’s nose.
CO2 recapture
Brewing already creates a lot of CO2 as a byproduct of the fermentation process, and some brewers are creating their own beverage-grade carbon dioxide with CO2 recapture systems.
Just like it sounds, these units capture the CO2 produced naturally as a gas by yeast during fermentation, and for most breweries, that pollutive CO2 is just released into the atmosphere. Why not recapture it, store it as a liquid, repurpose it around the brewhouse and become a more eco-friendly and efficient brew business? It’s worked for Grey Sail Brewing Co. in Rhode Island.
“I definitely recommend the CO2 recovery system,” said Alan Brinton, founder of Grey Sail Brewing, which added a unit last year. “It’s helping us to wade through the supply shortages. We have a CO2 recovery system from Earthly Labs. It cost $100,000. We use the recovered gas throughout the facility. It has helped us to lower our need for commercial CO2 but not eliminate it. I expect the ROI to be about five years.”
Grey Sail Brewing is Rhode Island’s southernmost brewery, located in the beautiful seaside town of Westerly, and sustainability is a core focus. As mentioned, Grey Sail Brewing implemented technology from Earthly Labs — a plug-and-play system called CiCi. Earthly Labs, which was bought by Chart Industries late last year, is one of the leading providers for small, craft brewery-sized CO2 recapture units, teasing quick installation, fast payback and a cloud-based software solution with real-time CO2 capture insights.
Since its inception, Earthly Labs has included Chart cryogenic CO2 storage tanks, vaporizers and regulators as a standard part of its offering to customers, so it made sense for the two companies to partner.

“Brewers are obsessed with the best ingredients to power their beer,” explained Amy George, president at Earthly Labs. “The ingredients brewers use actually power natural CO2, so it is a closed loop recycling process that is locally made, reducing dependence on outside sources, making great beer even better. Someday, CO2 capturing will be as common as solar, and of equal importance as a solution to combat climate change.”
How does CO2 recapture work?
Earthly Labs’ CiCi unit captures CO2 through a three-step process:
- Drying the gas to remove moisture;
- Scrubbing the gas to remove volatile organic compounds (VOCs) and other impurities; and
- Chilling the gas to below -34.7 °C to convert the gas to a liquid.
During commissioning, Earthly Lab techs will install piping and piping manifolds, tie in CO2 capture equipment to a fermentation tank, set up remote monitoring software, and train the team to capture and liquify CO2.
CO2 Pro Tip: Let’s talk kegs. To maintain the integrity of craft beer’s carbonation in a keg, temperature and applied pressure from the draft system must be considered. For instance, if too much pressure is applied to the keg, the keg will become over-carbonated. Learn tons of great facts about proper keg CO2 management in this Draft Beer Carbonation PDF from the Brewers Association.
“The best place for a CO2 recovery system will vary by brewery, but out of the flow of traffic and close to where most of the CO2 is made in the fermentation cellar,” suggested George. “We have minimal other infrastructure, with exception of an upgraded foam trap and CO2 tank for recovered CO2. An Earthly Labs CiCi Oak installation takes about three core days with one day of piping installation.”
Earthly Labs is not the only manufacturer of these recapture units. Pentair’s CO2mpactBrew is a “CO2 recovery plant” designed for craft-sized breweries with capacities from 50,000 to 35,000 hl/yr. It comes on a 40-ft skid or a well-ventilated 40-ft container for outside mounting, so it’s a beast.
Maui Brewing Co. was one of the first brewers to have a CO2mpactBrew plant installed. This recapture unit reduced Maui’s CO2 emissions by over 600,000 lbs in the first year alone, according to Founder Garret Marrero in this case study. The brewery noted via email that the unit creates about 100 lbs of CO2 when in operation and estimated it produced about 5,000 lbs a week or 20,000 lbs a month.


“Producing on an island, our CO2 supply is always limited, so we invested and continue to invest in a system to help offset the dependance we have on our suppliers,” said Kim Brisson-Lutz, VP of operations at Maui Brewing Co. “We have a CO2 recovery system, and we will be installing new technology called AirCapture to also produce CO2 for our facility. AirGas Oahu is our supplier. Typically, there are multiple suppliers for brewers to choose from. We only have limited suppliers here and choose to find alternative ways to provide CO2 to our facility through our CO2 recovery system.”
Based in Oakland, AirCapture is a leader in the direct air capture industry. The company’s onsite, modular DAC units harvest CO2 from the air or fermentation tanks, then make it available on-demand, for use in everything from breweries to greenhouses. I highly suggest listening to Bob Wilson, cofounder and head of sales and strategy at AirCapture, discuss the technology right here.
Pros and COns
Like everything in life, these units have pros and cons. In this same Brewers Association webinar on CO2 (teased above), Walker Modic, sustainability specialist at Bell’s Brewery, is asked his opinion on CO2 recapture units. He notes it’s definitely about doing the math, measuring the cost and operation of the unit vs. purchasing CO2 in your region. Brewers must not only take a hard look at the amount of money it takes for compression and storage, but also the brewery-wide modifications required to capture CO2.
“You need to be able to control the vent and collect events,” he said in this video, also noting, “the quality of CO2 is not always good enough for capture.”
Here’s Max McKenna, senior marketing manager at Boston-based Dorchester Brewing Co., also discussing quality. Dorchester has invested heavily in nitrogen as a CO2 alternative, but it’s still a little wary of CO2 recovery systems.
“In addition to the nitrogen generator, we have looked at CO2 recapture systems, though from what we’ve seen, it quite frankly hasn’t been worth it from an ROI and cost perspective, nor from its potential negative impact on the quality of the beer,” said McKenna. “Members of our team have worked places that do CO2 recapture, and even once the system, which is very expensive to install, was in, it ended up negatively impacting some of the beers during and after fermentation.”
“I do have some questions about CO2 recovery in terms of how much you’re needing to filter and compress and chill that CO2 to turn it into a liquid,” said Skypeck. “There are questions in my mind that haven’t been answered in regards really to how sustainable they are in terms of energy use. I’m sure that there are places where there are breakeven points, where, you know, that energy that you’re going to be putting into capture and process that CO2 pays for itself. That’s probably not a bright line because CO2 is way more expensive in some regions than it is in others, and energy’s way more expensive in some regions than it is in others. But all that said, if you’re a brewer and you can’t get CO2 surety of supply, it can be very, very meaningful.”
The demand for these units is there. Tröegs Independent Brewing is a 25-year-old craft brewery located in Hershey, Pa., and it has a contract for bulk CO2 supply from a large, nationwide supplier. That supplier just isn’t meeting the brewery’s CO2 needs, causing Tröegs to shut down production entirely for days a time (and Tröegs packages beer five days a week).
“We are planning on installing a CO2 recovery system in 2023,” said Andrew Dickson, production manager at Tröegs. “The recovery system should meet most, but not all, of our usage needs. We will still need to purchase CO2, but we are also installing two new storage tanks to increase on site CO2 storage in case of supply disruption.”

Questions to ask
Questions definitely need to be asked and facts need to be gathered. George and Earthly Labs have kindly provided a nice outline. If you are considering a CO2 recapture unit, we highly recommend you track down this information:
- Conduct a CO2 assessment to evaluate how much CO2 you naturally produce and the size of the system you will need.
- Review customer case studies or videos on successful installations.
- Evaluate how your supplier works to ensure your customer success and key metrics.
- Confirm the suppliers’ post-sale support processes from remote monitoring to post-sale service.
- Investigate if the partner’s organization reflects the values of your company – quality, sustainability, diversity, inclusion.
- Investigate the company size and scale to ensure longevity of support for the long-term. Can the supplier scale solutions to meet your growth.
“The CO2 industry is forecasting CO2 shortages that will continue, driven by supply and wells being turned off,” said George. “Demand of CO2 continues and incentives in the Inflation Reduction Act will drive prices up. Soon, craft breweries will be treating CO2 capture as an essential piece of equipment producing a key ingredient, not an extra step that would be optional if you have time in your brewery day. The ROI used to be two to three years on average, but with the shortages and revenue loss, it can be one to two years.”
Click here to see other CO2 Shortage articles.
The Last Word: Odell Brewing adds CO2 recovery system to Fort Collins, Colo. brewery

In October, Colorado craft brewery Odell Brewing Co. announced a major step forward in carbon reduction with the addition of a CO2 recovery system to its Fort Collins brewing facility.
As we’ve discussed many times throughout this series, breweries of all sizes utilize or produce carbon dioxide in various parts of the production process — as a natural byproduct of fermentation that enters the atmosphere, and then again to re-introduce CO2 to finished beer in the form of carbonation. This unfortunate double dip in CO2 consumption requires that it be both produced and purchased.
Odell’s new CO2 recovery system not only nearly eliminates the venting of CO2 to the atmosphere but also reuses it in the finished beer while eliminating the carbon emissions of producing and shipping finished CO2 to the brewery.
“Throughout our 30-year history, we’ve consistently and deliberately re-evaluated our processes and production materials looking for opportunities to create better, more sustainable practices,” explained Plant Manager Matt Bailey. “Without a doubt, CO2 reduction is one of the most meaningful ways we can reduce our carbon emissions and help our planet.”
Odell Brewing anticipates that within one year this new recapture system will prevent 1.4 million lbs of CO2 from entering the atmosphere. Per EPA calculations, that equates to the annual carbon emission of 70,000 gal of gasoline. Installation of the system has already begun, and the brewery expects it will be fully operationalized by April of 2023.
“To us, sustainability means having something that can carry on past our generation, and that’s what this really is,” explained Bailey. “After the seven-year mark, we see the financial return, but a project like this doesn’t fit traditional ROI calculations. Our return is closing the loop and putting more value on our planet and our future.”
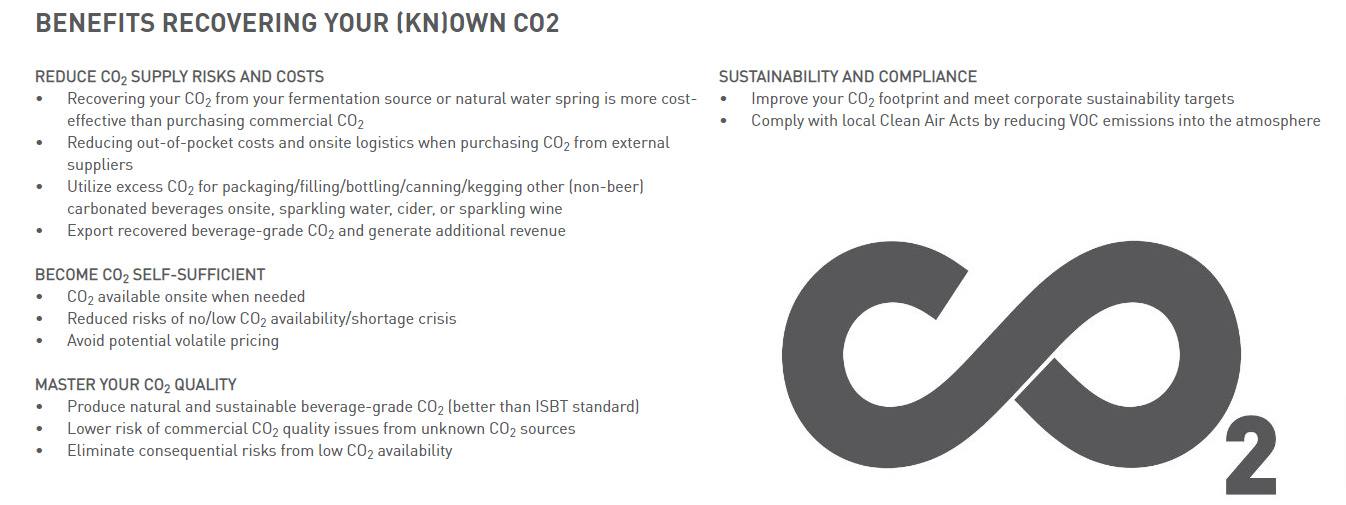
To achieve these carbon reductions, Odell has partnered with Pentair out of Denmark, which has spent many years engineering and developing equipment that’s scalable to breweries of Odell’s size. We summarized its products above.
“We are proud to be working in close partnership with Odell Brewing Co. as their CO2 recovery solution provider,” commented Pentair North American Director of Sales Molly Tsipis. “Our CO2 recovery plant, Pentair Haffmans CO2mpactBrew, is enabling Odell Brewing to become CO2 self-sufficient, a critical strength in the current CO2 supply landscape. By generating their own continuous supply of CO2 with Pentair Haffmans CO2mpactBrew, Odell Brewing can contribute toward a sustainable future while avoiding volatile pricing, supply risks, and quality issues.”
Leave a Reply
You must be logged in to post a comment.