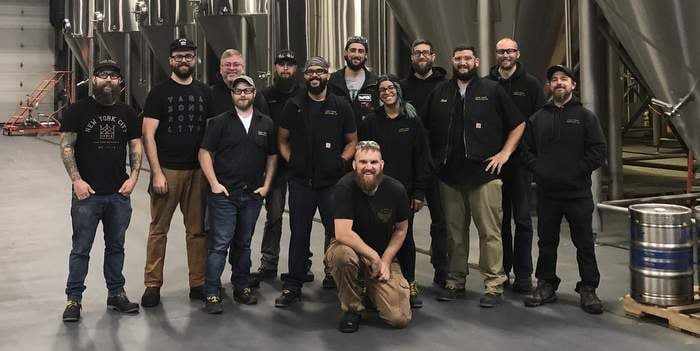
What is now the thriving Lord Hobo Brewing Co., located just nine miles north of Boston in Woburn, Mass., was an empty, cavernous 49,000 square foot warehouse just four years ago. With the vision of owner Daniel Lanigan, the vacant shell was transformed into an impressive, fully functioning brewery, opening its doors in June of 2015 and producing 5,000 barrels the first year.
Lord Hobo’s mantra is “to bring the New England craft beer experience to thirsty fans everywhere – Lords and Hobos alike – we all deserve to drink like royalty.”
Fast Start
The team was aware of the important role of the cooling loop in the brewing process, but the ambitious start-up was purposely planned as an inexpensive short-term means of getting the brewery operational.
“The goal was to be up and running as quickly as possible,” explains John Irwin, Lord Hobo’s Maintenance and Facility Manager. “So a small PVC glycol system was installed along with a 20 ton chiller. This allowed production of the first ales within a few weeks after starting construction of the facility.”

After tripling in size after just two years of business, Lord Hobo was named by the Boston Herald (06/01/2017) as the fastest growing brewery in America. Because of this lightning speed expansion, the PVC glycol cooling system quickly became over-taxed.
“With just a 300 gallon reservoir and small three-inch trunk lines coming out to supply 15 tanks, it simply didn’t have the flow or the cooling capacity to keep up with the growth rate,” explains Irwin. “Especially after 20 more tanks (much larger than the existing) were added. We knew the PVC system was not a life-time solution for the glycol run at the cold temperatures required. It becomes brittle and fails. Changing cooling systems was something that had been planned for early on and we fully expected to continue beer production during the upgrade.”
The search for the upgrade
When looking into the available solutions on the market that could be used for the new loop, they considered four methods of installation: welded/threaded steel and copper, solvent cemented and fused plastic.
Irwin, who has been a plumber for about 20 years before joining Lord Hobo, was used to design and piping installation. “I’ve been putting pipe and fittings together for what seems like forever. When I came onboard with Lord Hobo, I was asked to help find and install a new cooling system, and with the help of a couple ‘willing to do whatever it took guys’ who had never hung a stitch of pipe in their life… WE KILLED IT!”
The Lord Hobo team was hesitant to use steel pipe because of weight (about 50% heavier than plastic pipe), corrosiveness and needing the extra step of insulating and jacketing the pipe, which is expensive and time-consuming. Though fairly cheap, its heavy bulk created an unwieldy installation challenge and would require welding in a fully operational facility above equipment that was in use every day.
Copper, although lighter in weight than steel, was not only a more expensive product, but like steel would incur the additional cost of insulating and jacketing the pipe. “With a three-man crew, we figured that once the pipe was installed it would take almost as much time to insulate and jacket it, and that just wasn’t in the picture for us,” says Irwin.
A butt fusion plastic piping system was also considered. “For the large 8” size pipe needed to get to the next level of production, the heat fusion process would require a massive hot plate, basically the size of a large pizza that would be used on a scissor lift 40 feet in the air,” says Irwin. “It sounded like a cumbersome and possibly risky install that just didn’t make sense.”
Still with all these questions in his mind, Irwin attended a Master Brewers meeting, where he learned about COOL-FIT ABS Plus from GF Piping Systems – a pre-insulated plastic system joined with solvent cement. “After learning more about the system at the actual seminar, I was sure which system we’d choose.”
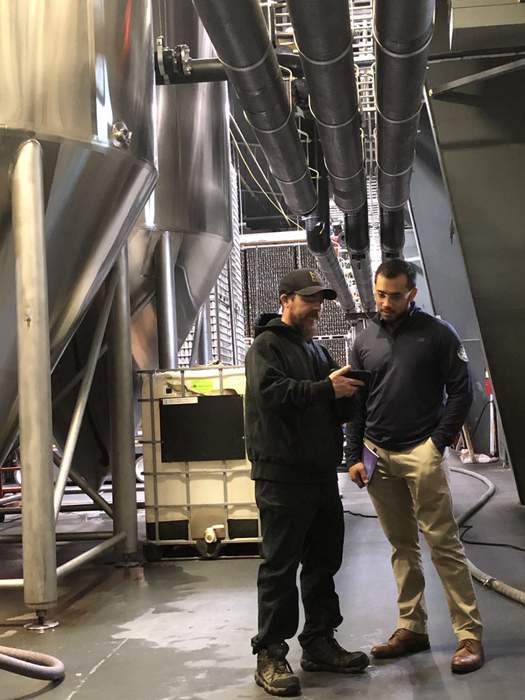
Irwin became convinced that COOL-FIT would be the best possible solution due to its readily available fittings, pre-insulation that required no extra costs, and history of success in similar applications including other breweries. Additionally, the system was simple to install.
Some more research was done and Lord Hobo’s team made the decision to go ahead with COOL-FIT ABS Plus for their glycol loop. After a day of training by the manufacturer, the crew installed 800 ft of d225 (8”) and 250 ft of d110 (4”) without interfering with brewery production. At the same time, a 200 ton chiller was also installed and a 3,000 gallon reservoir (compared to their previous 300 gallon size reservoir).
The COOL-FIT system installed at Lord Hobo conveys glycol at 28°F through the system to maintain the tank farm fermentation process, which includes 44 vessels in 160 BBL (24), 80 BBL (12) and 10 BBL (8).
“The installation was a great success and went as smooth as it could” sums up Irwin. “The GF transition fittings we used to connect the COOL-FIT ABS Plus to some existing copper and threaded pipe areas were easy to use and connected smoothly and effectively. We made roughly 450 joints and ran almost 1250 feet of pipe with hundreds of fittings. Maintenance onthe system is next to nothing… just a daily walk through to visually check the lines. Temperature loss in the system is virtually non-existent and the COOL-FIT pipe remains accessible but hidden.”

The company’s main building houses beer production and tasting room with more than 25 types of craft beer on tap, café with full kitchen offering a variety of creative pizzas, salads, and snacks, along with whatever is happening sports-wise on Boston TV, plus a gift shop with specialty everything Lord Hobo. Cold storage and office space is located across the street in a separate 14,000 square foot structure. Within the next two – four years, the Lord Hobo team plans to complete the tank farm of 11 rows, 7 deep. 77, 160 BBL vessels, and as many 10 BBL tanks as they can squeeze into their place.
In anticipation of that, the COOL-FIT system is already installed with valves in place ready for hook-up. Irwin is proud of the fact that they never lost a day of production doing the COOL-FIT install.
“We never interfered with operation or disrupted production,” says Irwin. “We wouldn’t have been able to do that with steel pipe, because we’d have had sparks flying everywhere. Welding right above our brand new multi-million dollar canning line would have meant stopping production to protect the equipment.”
Even though the install team was a small crew of three that completed the work, they had the help of the whole Hobo team when needed. “It was a great team building experience because it got everyone involved and now everyone feels like a part of that project,” says Irwin. “It was really amazing to see the whole thing come together.”
By the end of 2017 the brewery was producing close to 20,000 barrels a year and in its third year reached 32,000 barrels, an astonishing 420% growth rate. In 2019, the Lord Hobo team anticipates stepping that output up to over 50,000 barrels.
Angela Sampaio is a Market Segment Manager, Cooling (Eastern region) with GF Piping Systems.
Leave a Reply
You must be logged in to post a comment.