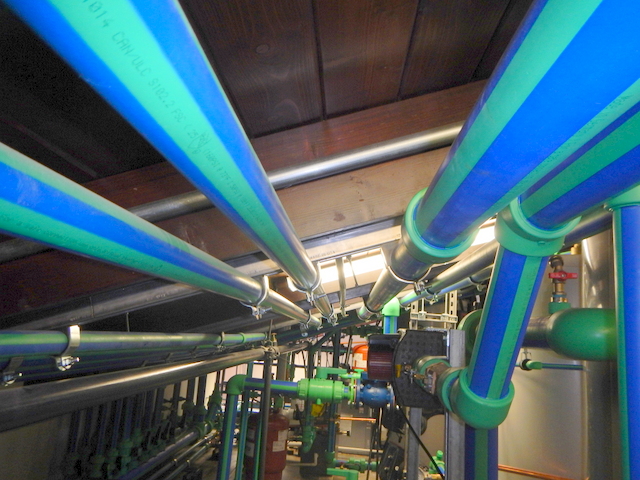
There is a lot to appreciate about Flathead Lake Brewing Co.’s (FLBC’s) newest brewery and pub house in Bigfork, Mont. There is the award winning beer, which can be enjoyed while gazing out over the largest natural freshwater lake west of the Mississippi. There is the facility, a rustic yet welcoming spot, borne from the ruins of an old bowling alley. Finally, there are the many sustainability strategies used in the construction and functionality of the brewery. Most notable among these is the unprecedented use of clean effluent from a nearby water and sewer treatment plant to indirectly provide heating and cooling for the building and brewing processes.
The keyword is indirectly. The effluent, which is piped into the brewery from the neighboring Bigfork Water and Sewer District, is completely contained within a separate closed loop. It serves the typical role of a geothermal well field, something that was not possible for the brewery to install given its downtown location. The effluent is the “heat-sink,” giving up or absorbing heat as needed in order to pre-heat or pre-cool the water used for heating and cooling the building and the glycol that is used in the brewing process.
It is a complex design that uses several thousand linear feet of Aquatherm Blue Pipe to transport both heating water and glycol to and from several water-to-water and water-to-air WaterFurnace heat pumps. A plate and frame heat exchanger is positioned between the closed effluent loop and the actual fluids used for heating and cooling. Before the water reaches the heat pumps it is pre-heated/pre-cooled via a plate & frame heat exchanger using the clean effluent. It is then routed through a Lochinvar buffer tank, which serves as a reservoir of pre-tempered water to be used downstream for HVAC and process applications.
A fitting choice
JE Engineering Inc. of Kalispell, Mont., designed the mechanical system, accumulating numerous points toward the owner’s goal of LEED Gold certification.
“The building was designed to be as energy efficient as possible,” said lead designer, Tom Kientz, of JE Engineering.
Efficiency was a challenge given all that is occurring under the roof of this particular brewery. Hot and cold setpoint temperatures must be maintained on various loops serving the building HVAC, snow melt system, fermentation tanks, keg coolers, brew kettles and more. It’s a lot of piping and a lot of fittings, almost all of which are Aquatherm — a strategic choice of material for many reasons.
“I don’t think we could have done it any other way. Aquatherm was by far the best choice,” said Jeremy Waters, chief operating officer of Van Dort Heating Inc., the mechanical contractor on the project.
Waters explained that the heat fusion process used to connect the Aquatherm piping systems saved an extraordinary amount of time and money.
“With Aquatherm you can drill into the pipe and with a fusion socket assemble your own reducing tee or manifold out of actual pipe. With copper you have to weld in a fitting, and a single 4-inch copper tee might cost $300 to $400. On a job like this, that could add $100,000 to the piping and installation costs alone.”

The Van Dort team worked closely with local Aquatherm manufacturer’s representative Ridgeline Mechanical Sales (Bozeman, Mont.). Ridgeline, which has offices throughout the Northwest and a reputation for detailed product knowledge and support, works hard with the stocking distributors in the Kalispell area to promote the product and provide training and support for the users and specifiers of Aquatherm.
Van Dort used both socket and butt fusion to assemble the complex network of piping. The contractor used McElroy Spider equipment for fusion installations of Aquatherm pipe and fittings that were 2-inches and larger. This device features a worm gear drive with parallel link system to bring pipe and fittings together evenly and under control. For smaller pipe sizes, Van Dort used socket fittings and hand-held welding irons to join pieces of pipe together.
Clean, reliable and sustainable
Cost wasn’t the only thing about Aquatherm Blue Pipe that made it appealing for this particular job. Robert Millspaugh, operations supervisor at FLBC, did extensive research on what piping to use for the process side of the brewery.
“We were looking for products that would help us achieve a LEED certification and Aquatherm had a lot to offer. I also came across an article on Epic [Brewing Co. in Salt Lake City] and how they used Aquatherm in a renovation and discussed the product with the brewer there,” said Millspaugh.
Millspaugh began to discover that Aquatherm was fast becoming the piping system of choice among microbrewers throughout the country. One of the biggest reasons for this trend is the fact that Aquatherm does not require any glue or solder on pipe joints. The heat fusion process used to join pieces of Aquatherm pipe together eliminates the need for either.
Heat fusion works by using welding irons or a heating plate to melt the connection points of the piping components to be joined. This allows the polypropylene chains to join together as the connection cools for a permanent bond, as if they were one solid piece. This seamless connection prevents any sort of chemical or physical weakness at the point of connection and results in a much lower instance of leaks or failures. The end result is a connection that is just as strong (if not stronger) than the pipe itself.

Millspaugh, J.E. Engineering, and Van Dort Heating were all on the same page when it came to choosing Aquatherm for many reasons, including:
- Aquatherm fit in well with the sustainability goals of FLBC (e.g. it is completely recyclable, requires no adhesives or solders that emit fumes, and has no VOCs).
- The fusion method is cleaner and more reliable than traditional metal pipe connections.
- Aquatherm offered many opportunities for indirect LEED credits.
- The natural insulating properties of Aquatherm Blue Pipe enhance the efficiency of cold systems like the glycol processes used to brew beer.
- Aquatherm marries well with renewable energy sources like geothermal.
More than just a pretty pipe
When brewery patrons aren’t enjoying the lake view they can look through glass partition walls right into the brew house and see the impressive display of blue and green striped pipe, ranging in size from ½ to 4 inches. They may not realize it, but all that pretty pipe is transporting the very fluid that keeps them warm as they dine in the restaurant, or enjoy a beer flight in the tasting room. It’s what transports the Btus from one place to another so that the fermentation tanks hold the perfect temperature to craft an award-winning IPA. It even helps keep the sidewalks clear of snow when it’s time to go home.
Barry Campbell is the vice president of advertising and media relations with Aquatherm, based in Medina, Ohio (not too far away from CBB headquarters). Before graduating from Ohio University’s E.W. Scripps School of Journalism with honors, Campbell had already launched a professional writing career as a reporter and working for the Associated Press. His career spans three decades, including award-winning work in the newspaper, trade magazine (with a more decade in HVAC), and marketing/advertising/PR fields. As Aquatherm’s VP of marketing, Campbell provides a unique perspective on all media-related and marketing matters and works tirelessly to educate North America about the benefits of polypropylene-random pipe for P/HVAC and industrial applications.
An Aquatherm case study at Flathead Lake Brewing https://t.co/k1ORykQChy via @craftbrewingbiz
Interesting article from my hometown brewery! An Aquatherm case study at Flathead Lake Brewing https://t.co/Dbk7OEFySJ
Kudos to our local brew pub for their commitment to sustainability. @FlatheadBrewing https://t.co/HCZkWTnB33
RT @CraftBrewingBiz: A pipe runs through it: An @Aquatherm case study at Flathead Lake Brewing. @FlatheadBrewing https://t.co/6y3NMXj5ll ht…
An Aquatherm case study at Flathead Lake Brewing https://t.co/Z3aLh7lZzP via @craftbrewingbiz
LVRGLLC: #CraftBeer #CraftBrewing #Beer #BeerBiz A pipe runs through it: An Aquatherm case study at Flathead Lake … https://t.co/g8ZrFxS9kc
#CraftBeer #CraftBrewing #Beer #BeerBiz A pipe runs through it: An Aquatherm case study at Flathead Lake Brewin… https://t.co/0Z7lpWRvjb